As silos once dotted the landscape of dairy farms across the U.S., today “methane digestion tanks” are a trending feature. In the interest of reducing methane pollution and establishing a revenue stream for a renewable resource, dairy and livestock operators are creating mechanisms to produce renewable “biogas,” also known as compressed natural gas (CNG). The systems of production generate a renewable fuel source of biogas and fertilizers for soil restoration as well as introduce new planning hazards to rural communities.
The use and transport of liquefied petroleum gas (LPG) and propane have been regular parts of the rural landscape in support of agriculture operations. However, compressed natural gas (CNG) introduces new hazards in the increased volume of production, the frequency of transport, and additional security challenges (e.g., anhydrous ammonia, ammonium nitrate, fuels, and equipment as targets of theft in rural areas, usually among drug users and suppliers). These hazards should be included in emergency management planning and training.
Compressed Natural Gas
Methane, also known as CH4 or natural gas, is the odorless, colorless gas used for heating, cooking, and industrial power generation. In this form, it is scented with mercaptans, which smell like rotten garlic or cabbage, for easy detection and hazard mitigation by consumers and emergency responders before a flammable range is reached. Methane can be encountered during excavations, dissolved in groundwater, released in oil and gas extraction, and enroute to refiners in interstate pipelines.
While liquefied natural gas (LNG) requires, CNG is commonly transported in commercial and fleet vehicles. ). While planning for CNG hazards, understanding its properties is essential. These are outlined in the safety data sheets and the U.S. Environmental Protection Agency’s Computer-Aided Management of Emergency Operations (CAMEO), a system of software applications used to plan for and respond to chemical emergencies.
On-Site Production
There is an entire . Dairies across the U.S. are implementing similar technology. Transformation of CNG into a renewable state starts with the collection and digestion of manure in large low-pressure membrane tanks. Gases collected from this process are routed through an absorption system, which then scrubs the methane of any impurities—such as volatile organic compounds, hydrogen sulfide, and ammonia—and prepares it for use.
The on-site production system may also have an on-site burner or vent for removal of impurities and prevention of release into the atmosphere. This burner is often mistaken for a fire on the farm by the public, which creates frequent good-intent 911 calls by the public. Authorities with jurisdiction should have a thorough understanding of the process, risks, and safety features. Planning should include site visits on construction and startup, and the site should be included in emergency pre-planning, exercises, and training.
These processes are often remotely managed. Therefore, it would not be unusual for a system manager three states away to dispatch a local representative, who will arrive after responding agencies. It is important to have and maintain these contacts as part of the emergency action plan. While transport methods are standard, equipment is variable between sites and evolving. This complicates the familiarity with each hazard.
Transporting Biogas
The methane recovered from the renewable process is shipped in various ways. Dairies located near a gas pipeline establish a point of sale or pipeline connection where the gas is compressed and put into larger pipelines. Some dairies pipeline CNG to a dairy with the sale point. Others power on-site generators for local use.
If the facility does not have ready access to a sale line or a means for on-site use, the gas must be compressed, loaded, and transported by truck to a sale line for pipeline distribution or directly to a power generator. Fleets of these trailers in operation have been dubbed a “virtual pipeline.” At the same time, as local dairies truck and pipeline CNG to a dairy with a larger pipeline connection, CNG trailers from other mid-stream oil operations are being trucked to local oil and gas exploration sites, which use the gas as a cleaner renewable fuel while developing oil and gas wells that power generation and water heating plants. CNG renewable and extracted gas cross paths and share roads with farm equipment in the rural environment, introducing a greater potential for danger on the road.
While CNG can be transported by traditional means such as a straight truck, higher pressures and volumes required for economical transport require either a traditional compressed gas tube trailer or the new generation of trailers manufactured under U.S. Department of Transportation Special Permit (such as DOT SP 14951 trailers), which carry four times the volume of gas as the former. These trailers are unique, differ from traditional pressure trailer design, and require different approaches to hazard mitigation.
DOT SP 14951 trailers are constructed of lightweight engineered composite mounted in sets of four tanks plumbed together to a common manifold. The tanks are set in metal framework, not unlike intermodal tanks. While the outside skin or weather-cover of the enclosure can be metal, this permitted construction type uses a polymeric canvas drawn down over the sides. Once covered, the trailer resembles a typical cargo trailer. They are equipped with a GPS tracking system for operations and security monitoring.
The design has a resettable pressure reduction device and is equipped with remote shutoff valves that, when manually activated, stop gas going in or out of the trailer manifold. Fire protection involves a shaped alloy wire that, when heated above 226° F., shrinks, venting the entire volume of all four tanks through the roof or top of the trailer to reduce the likelihood of a “dynamic rapid release event” when involved in fire.
This safety feature has released all gas completely in under an hour during previous incidents, but it creates a significant vertical fire column if ignited. This presents challenges if the trailer is on its side or roof after a rollover or if it vents under structures, such as a bridge.
Power Consumption
CNG is a clean alternative fuel that, with new transport technology and applications, is rapidly expanding across a variety of markets and geographies. In rural Galeton, Colorado, it has replaced LPG and diesel for water heating and power generation. In oil and gas fields, it powers hydraulic fracturing directly and by generating electricity on-site. Emergency planning must include hazards presented by all three fuel types (CNG, LPG, and LNG) as they may be used alternately to meet seasonal air quality requirements. Each on-site power generation or water conditioning operation consumes as much as one trailer of CNG every two hours, creating a steady flow through the jurisdiction.
Planning for Emergencies
Emergency managers and responders can address the challenges presented by the production of CNG with these steps:
- Identify the sites producing CNG within and surrounding a given jurisdiction. Some jurisdictions trigger thresholds for planning quantities; others do not. The planning and zoning review process as well as construction permitting may be the best points to identify facilities of this type. Exchange business cards now, not during an emergency.
- Determine the trucking routes for CNG trailers—perhaps the most dynamic aspect of the process. If they have not been established during the permitting process, then observation, especially in rural areas, will identify these routes easily due to a new and distinct placarded container traveling gravel roads. Following a placarded truck to its destination can reveal travel routes.
- Determine the destination. Some jurisdictions may have overlapping transport routes where CNG from two different sources at different magnitudes are headed to two different destinations on any given day.
A jurisdiction’s hazard mitigation plan and emergency operations plan should be reviewed with the operators of newer technologies, as with any company new to a jurisdiction operating with hazardous or dangerous materials. On site security must be taken into account, as with any facility with a large quantity of flammable fuels.
Local emergency planning committees, emergency management, and industry associations such as the Colorado Planning and Response Network (CPRN) or the Texas Pipeline Operators are great resources to help local jurisdictions.
Balancing Green Technology With Community Safety
Agriculture is an ever-evolving industry with an interest in developing new and varied revenue streams. Dairies have found an opportunity to reduce greenhouse gas emissions with a saleable renewable biogas. Green technology, for all its benefits, does not address inherent unintended hazards but creates new management pain points for emergency planners and responders. With this innovation comes the need for diligence, dialogue, and planning for new local challenges. Prevention, emergency action planning, and operator relationships will prepare and develop requisite awareness and skill sets of local responders.
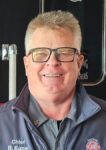
Russ Kane
Russ Kane, M.Sc., CFO, CWMS, is a fire chief in Northeast Colorado with the Galeton Fire Protection District. Chief Kane has four decades of progressive of fire, hazmat, and emergency services leadership in the public and the private sectors at the local, county, regional, and state jurisdictional levels. Specifically, Chief Kane has been involved as a responder and incident management team member on Type 3-1 incidents in rail, power, oil and gas, chemical industries, special events, and the 9-11 attacks, as well as western wildland fire mobilizations and campaigns. Since 1981, Kane has been working with the New Jersey Fire and Emergency Services, where he has enforced major environmental, health, and safety regulations for hazardous materials incidents. In his roles with the agency, he has developed perspectives as a responder and a member of the regulated community. In his present role as a rural fire chief in the fourth largest oil and gas field in the U.S and member of the Colorado Preparedness & Response Network, he manages potential jurisdictional conflicts through relationship management with oil and gas producers and the agricultural community.
- Russ Kanehttps://disasterpreparedness.kinsta.cloud/author/russ-kane